About Formula Electric at Berkeley
Formula Electric at Berkeley (FEB) is a 100% student-run team of UC Berkeley students that designs, builds, and races an EV racecar in annual competitions.
Industry: Automotive
Product: Formula EV racecar
Location: Berkeley, CA
Why Fictiv
Customer Challenges: Engineering students were inexperienced in designing, manufacturing, testing, and assembling an EV.
Fictiv Capabilities Leveraged
- CNC Machining
- Design for Manufacturability Analysis & Consultation
- Cost Down Guidance
- Materials Expertise
Results:
- Part weight and cost savings of 20%
- Best-ever competition ranking
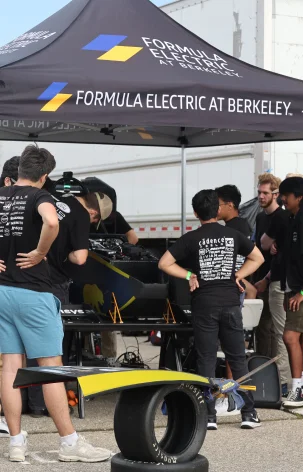
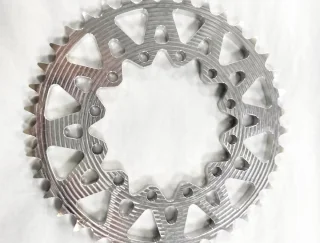
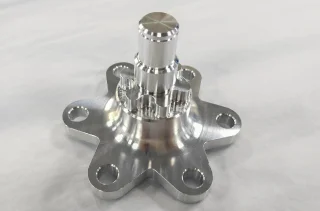
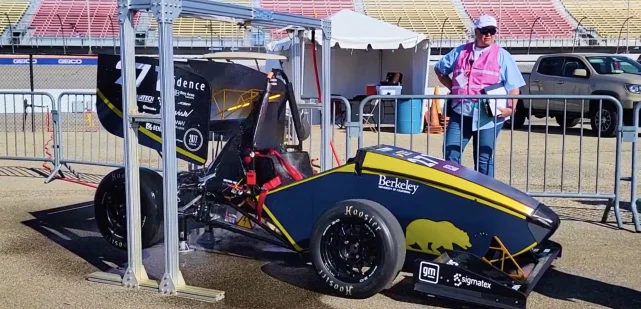
For the next generation of engineering talent, finding inspiration, excitement, and hands-on experience beyond the classroom can provide a critical head-start into their respective industries. The close-knit, dedicated team members of Formula Electric at Berkeley, who are competing in the Formula SAE Electric season (Society of Automotive Engineers), are a shining example of this. By partnering with the manufacturing experts at Fictiv, these engineering students have designed, manufactured, assembled, and tested their competition-ready electric vehicle built to race against other university student organizations. They were inspired and advised by Fictiv experts throughout the process, but the entire enterprise was driven by students. This is their story.
Formula Electric at Berkeley
Formula Electric at Berkeley (FEB) is a unique student-led organization dedicated to designing, building, and racing high-performance electric vehicles in collegiate competitions, such as Formula SAE Electric. This program, which is one of the largest and most diverse at UC Berkeley, provides the 160-plus students from more than 40 majors with hands-on experience in engineering, project management, vehicle building and racing, and teamwork, preparing them for careers and internships in automotive, aerospace, advanced technology, and beyond. The team’s focus on innovation in electric vehicle technology, including battery systems, electric drivetrains, and vehicle dynamics, sets it apart from other similar initiatives. More than 70 collegiate teams compete against each other in the annual electric vehicle racecar competition.
Caroline Johnson, team manufacturing lead, describes working on the EV motorsport team as “Taking our online ideas and turning them into real electric vehicles.” For these engineering students, it’s the opportunity of a lifetime, one that empowers them to apply their engineering knowledge beyond the classroom.
“For these engineering students, it’s the opportunity of a lifetime, one that empowers them to apply their engineering knowledge beyond the classroom.”
– Caroline Johnson, Manufacturing Lead, FEB
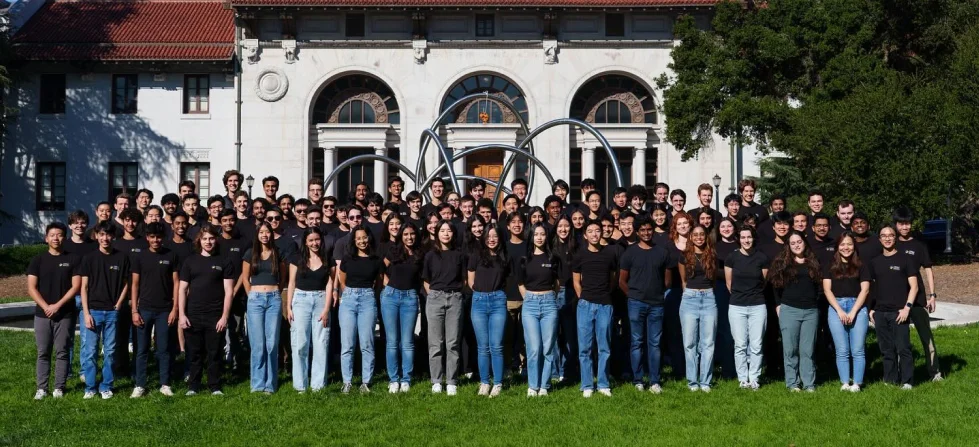
Mentorship & Inspiration
Part of this life-changing opportunity involves securing sponsors, like Fictiv, willing to offer mentorship and guidance on the design, manufacture, and assembly of mechanical parts that culminate in a competition-ready electric vehicle. Johnson says this: “That’s where sponsorships become so critical. Fictiv has been a great help for us, not only in providing our parts but also in mentoring.”
“That’s where sponsorships become so critical. Fictiv has been a great help for us, not only in providing our parts but also in mentoring.”
– Caroline Johnson, Manufacturing Lead, FEB
Team responsibilities are comprehensive and can be daunting. They include budgeting, project management, planning, design, funding, building, and testing EVs—all outside the framework of classroom, homework, and other obligations. So why participate in a rigorous, time-consuming activity without academic credits or official university direction? According to Johnson, participating in the team project and watching the final car pass inspection was “…one of the most exciting moments of my life.” Fictiv mentors agree.
For Samson Olanrewaju, Technical Applications Engineer at Fictiv, “Mentoring and guiding the students at Berkeley was so exciting. Seeing their enthusiasm, energy, and curiosity was inspiring and worth all the effort we put into this project. If I could teach students like this about engineering, I’d do it every day. I’ll always be proud of being involved in their journey.”
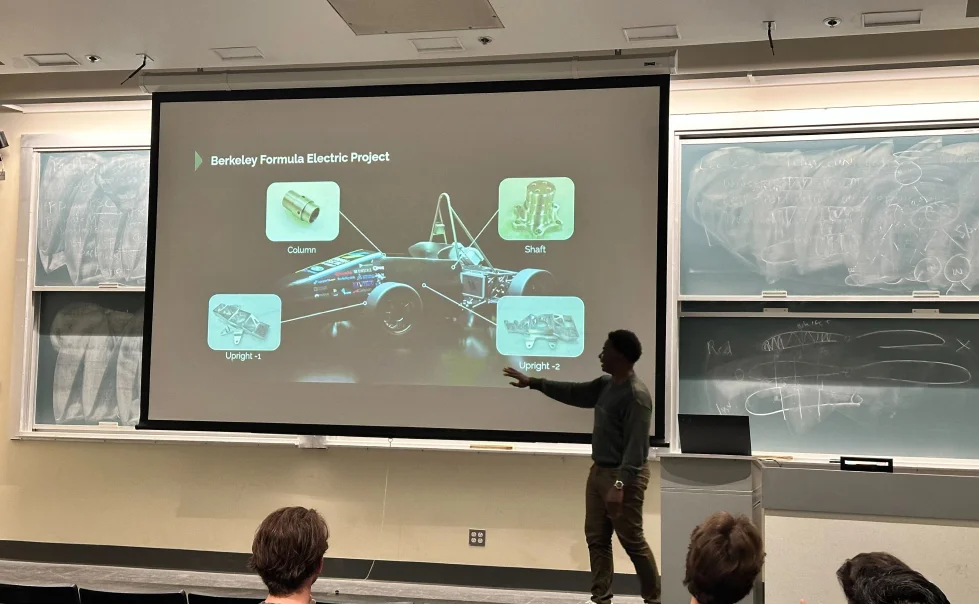
For Valentina Bocca, Senior Account Executive at Fictiv, “The Berkeley team is great to work with; they’re always responsive and eager to have Fictiv feedback.” Students often find internship opportunities and careers in leading companies in the industry, including Ford, Joby, and several EV and motorsports companies.
“Mentoring and guiding the students at Berkeley was so exciting. Seeing their enthusiasm, energy, and curiosity was inspiring and worth all the effort we put into this project.”
– Samson Olanrewaju, Technical Applications Engineer, Fictiv
Getting Started
With little or no manufacturing experience to build from, FEB students remained in regular contact with their Fictiv advisors. Olanrewaju provided detailed design for manufacturability (DFM) guidance. “We met bi-weekly for months. I had to give them the basics so they would understand this project’s complexity from a design standpoint. We provided many parts (detailed below) but mostly guidance.” Chris Leafstrand, the team’s chief engineer, agrees: “We’ve worked very closely with Samson (Olanrewaju) and Valentina (Bocca), and they’ve been very instrumental in building up our base of manufacturing knowledge for team members on the team, and those of us building a racecar for the first time.” He says, “We’ve been working with Fictiv since 2021, and they’ve been invaluable in educating and supporting us.”
“We’ve been working with Fictiv since 2021, and they’ve been invaluable in educating
– Chris Leafstrand, Chief Engineer, FEB
and supporting us.”
Fictiv advisors Bocca and Olanrewaju flew to Berkeley to give an in-depth presentation on the applied mechanical engineering involved in building an electric vehicle, including foundational education on the basics of CNC machining. According to Johnson, Olanrewaju taught her “…more about the manufacturing process than I learned in the classroom so that I could supplement my formal education with even deeper learning about engineering.” The session even drew students from other programs, such as the Space Technology and Rocketry (STAR) team.
Design for Manufacturability (DFM)
During the presentation, Fictiv advisor Olanrewaju explained the basics of DFM for their EV racecar. According to Olanrewaju, “The initial contact was to provide the students some DFM feedback because they were trying to manufacture the uprights for the vehicle (which hold the hub and allow the rotation of the wheel.)” Olanrewaju provided guidance in four areas: Part geometry, tolerances, and material selection.
The students’ goal was to maintain their design intent while cutting costs. They relied on sponsors to fund their efforts, so they wanted to optimize these project elements. Olanrewaju saw his role as “making sure the students’ parts were manufacturable. That involved extensive DFM guidance and strategizing.”
Building a Competitive Electric Racecar
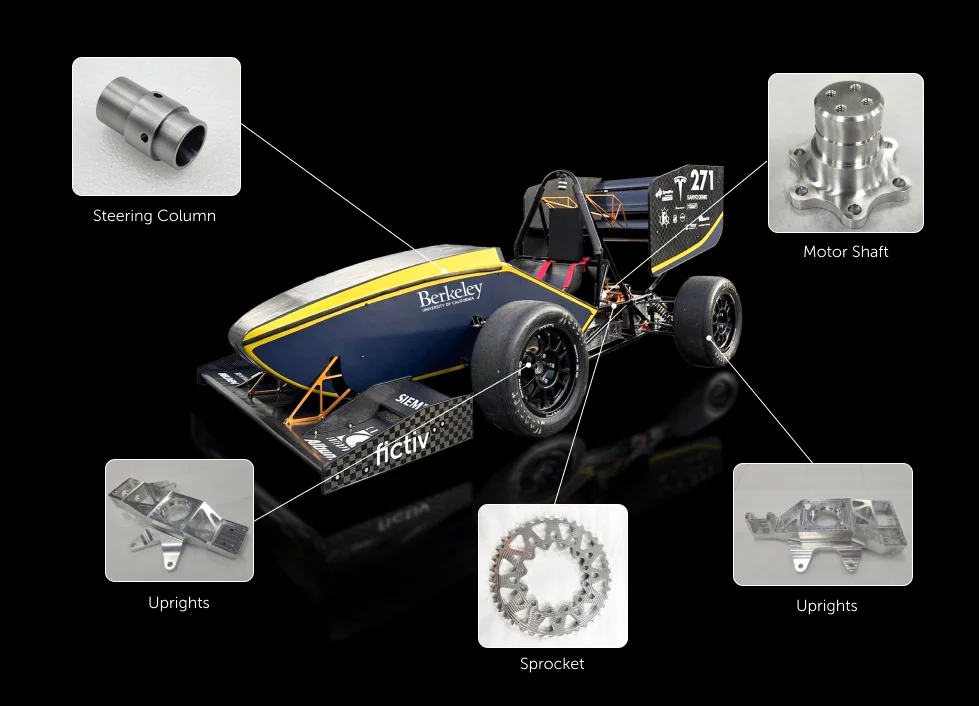
After initial work on the car, the students needed more hands-on guidance. Olanrewaju describes it this way: “It started as something basic, just once a month phone call. And then, as they began to wrap up and get closer to the assembly level, they needed more hands-on help from a technical expert. I started meeting with them bi-weekly and giving them feedback about necessary changes.”
For their third-generation car, the team had several opportunities to update or improve critical parts, including the driven sprocket and motor shaft, uprights, steering column, and battery structural bars. Each provided further opportunities to advance the students’ understanding of manufacturing considerations.
Sprockets & Splining
Challenges included finding the right sprocket dimensions so that it would engage with the chain to transmit rotational power. It was also challenging to find the right materials, weight, and tooth profile pitch to optimize the sprocket and ensure power transfer with minimal friction and wear. Splining was used to create grooves on the drive shaft to match the grooves on the sprocket.
“For this design to work well, we needed tight tolerances. When we got the result from Fictiv, we were amazed at how perfectly it fit.”
– Can Aydin, Powertrain Lead, FEB
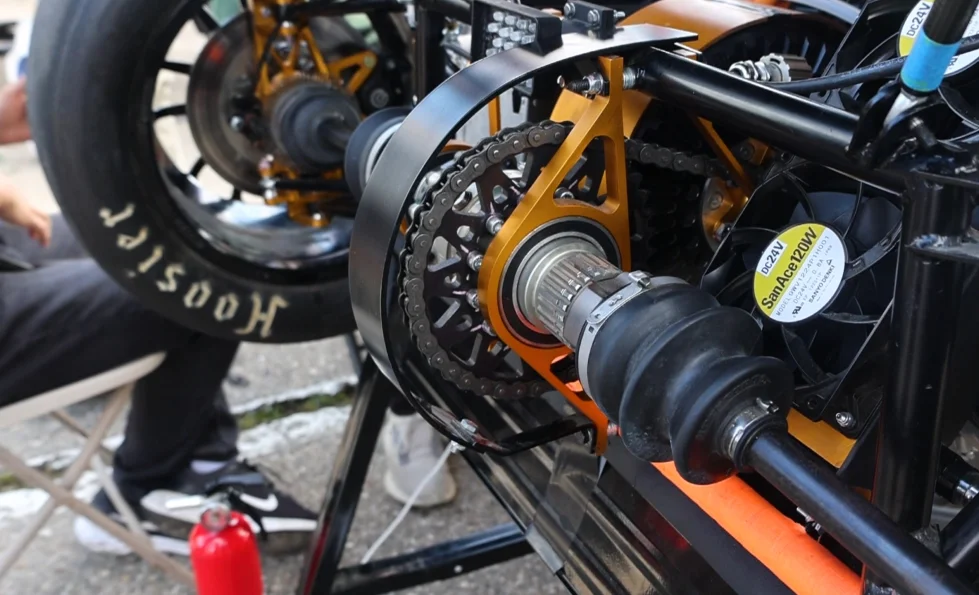
For Can Aydin, the team’s powertrain lead, working on the sprockets and splining was very educational. “We machined our sprockets in-house last year, so we didn’t have proper splining. That caused a lot of issues with our chain, where it would drop off and leave particles within the chain. This year, we got the perfect splining from Fictiv, so we didn’t have any issues.”
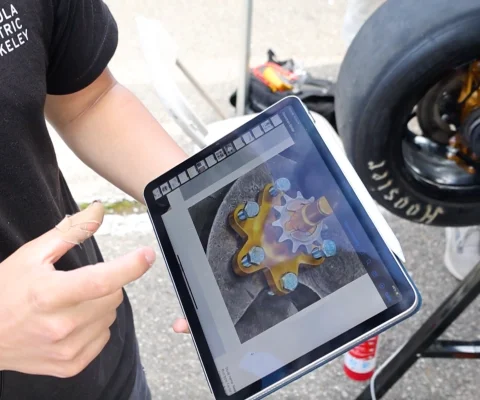
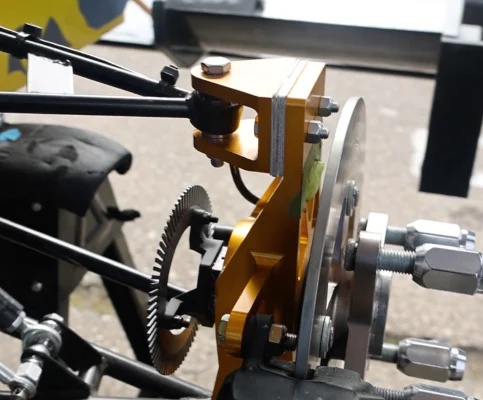
Olanrewaju: “The students had the driving sprocket and the motor shaft machine bifurcated, so they could make sure everything fit together. They utilized a flower shape pattern to maximize the tangent surface area to rotation.”
Aydin says, “For this design to work well, we needed tight tolerances. When we got the result from Fictiv, we were amazed at how perfectly it fit.”
Thinking Critically About Tolerances
Tolerances were a considerable challenge for the students. On the one hand, the driving sprocket and motor shaft needed to fit perfectly. On the other hand, the students could eliminate costs by dialing back the complexity and tolerances where they weren’t necessary.
Toshko Andreev, the team’s president, explains, “I think the main thing that changed the cost and the complexity was tolerancing. So, we spent a lot of time making these drawings and tolerating everything once we sent them out. And then on the call with Samson, he showed us how to think critically about which tolerances mattered. That really changed how we were manufacturing, which is great.”
Olanrewaju explains it this way: “Let’s assume you’re manufacturing a part with a tolerance of ±0.01, intended to mate with another part that has a tolerance of ±0.015. In theory, this should result in an acceptable fit. However, if the assembly involves rotational movement—like components in an automotive system—the looser tolerance could lead to unintended play or movement during rotation. To address this, we performed a tolerance stack-up analysis across the entire assembly, evaluating how individual tolerances accumulate and interact, part by part and between mating components, to ensure overall functionality and precision.”
This analysis was a collaborative effort with FEB to ensure that Fictiv could accommodate their needs. It involved a continuous back-and-forth process to balance design intents, reduce costs, and fine-tune materials and production methods. “All our calls and discussions were focused on ensuring the vehicle met performance expectations, ran efficiently, and gave them a competitive edge in their race,” says Olanrewaju. Reducing the weight of the parts and moving production overseas cut costs by 20%.
“This analysis was a collaborative effort with FEB to ensure that Fictiv could accommodate their needs. It involved a continuous back-and-forth process to balance design intents, reduce costs, and fine-tune materials and production methods.”
– Samson Olanrewaju, Technical Applications Engineer, Fictiv
Materials Expertise
The team also worked with Fictiv to produce the battery structural bars, which sit inside the battery casing and hold together all of the modules. Daniel Pack, the accumulator mechanical lead, says, “We had strict material requirements to ensure our battery was safe, including UL 94 V0 rating and being able to withstand 90° C temperatures. The great thing with Fictiv was we were able to propose different materials. This process went back and forth many times quickly, and we were able to optimize for a material that would fit our qualifications, hit our tolerances, and then also be able to ship on the timeline that we needed to build the car on time and get running.”
“We were able to optimize for a material that would fit our qualifications, hit our tolerances, and then also be able to ship on the timeline that we needed.”
– Daniel Pack, Accumulator Mechanical Lead, FEB
Assembly & Testing
The assembly and testing of the students’ EV was another critical aspect of the project. Olanrewaju states, “Technically, Fictiv could have done assemblies if they had requested it, but for this project, we specifically shipped discrete components. When the students received the parts, they undertook the assembly and testing themselves, gaining invaluable hands-on experience. This approach allowed them to delve deeper into the complexities of the production lifecycle—manufacturing samples/prototypes, testing, identifying issues, and then returning to refine their designs.”
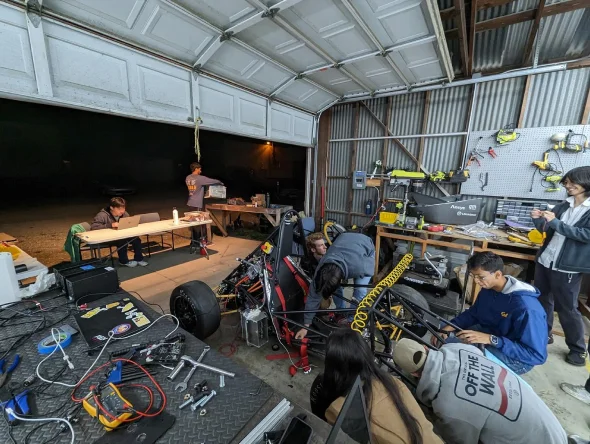
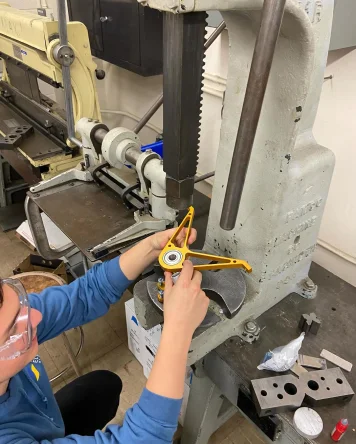
Olanrewaju goes on, “They discovered that it takes several rounds of testing to achieve the desired results, learning that things may not fit perfectly on the first attempt, and it usually requires multiple iterations and prototyping before reaching a successful outcome.”
The students would do the testing and then return to Fictiv advisor Olanrewaju to provide feedback about what they needed to change. They required close guidance for each design tweak.
Chris Leafstrand describes it this way: “We learned there are two types of assembly methods: Stationary assembly, where it’s bolted together, and locations that are bolted and fixed together without moving. And then there was a rotating assembly where it rotates while assembled.”
From Olanrewaju’s perspective, achieving smooth, vibration-free rotations was one of the most significant challenges faced by the student team. It required extensive testing and numerous calls, with ongoing adjustments to the design and manufacturing process. Through a series of iterations, the team fine-tuned the system until the car’s rotational components operated correctly without causing excessive shaking or instability.
He goes on, “The perseverance and collaboration ultimately paid off when they resolved the issue, ensuring smooth performance.”
Ultimately, the students got the car running and prepped for the competition, packing everything up and making the 40-plus hour journey across the country to Michigan International Speedway.
Competition: A Week of Firsts
The week of competition was the culmination of years of hard work (2024 represents the third-generation car built by FEB). For the Berkeley team, it was a week of firsts. “We got our car running for the first time just before the competition,” explains Johnson. “And we only had 30 minutes of testing time before we had to pack it up and send it to Michigan (the site of the Formula SAE Electric competition).” Later, the team began a series of required inspections and tests at the speedway to participate in the dynamic driving events. (Only half of the teams will successfully complete this portion of the competition).
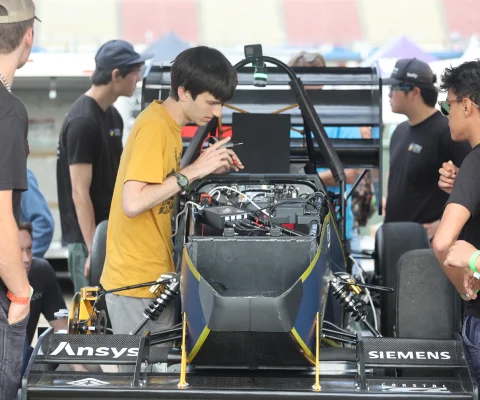
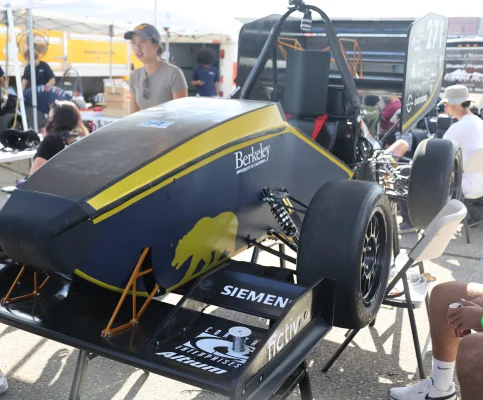
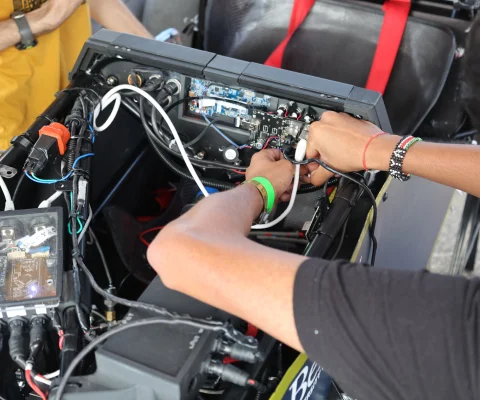
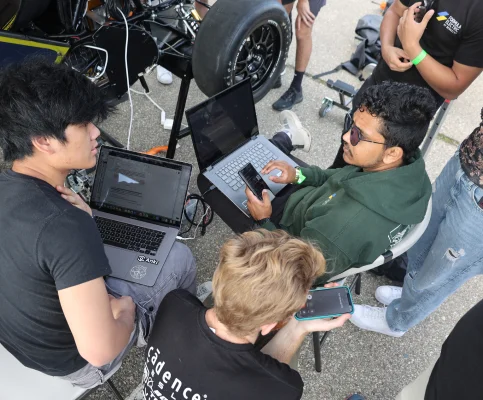
They later rallied to overcome a significant software challenge that had blocked further advancement until the morning of the final day. With hours remaining in the competition, the team racked up a series of first-ever passes, including the tilt test, where the car is rotated to a 60-degree angle to ensure it won’t flip over, and a rain test to ensure electrical safety.
Finally, the team saw their car run under its own power at competition for the first time at the brake test, where the car accelerates to 30 mph before braking. Unfortunately, brake issues halted further advancement in the competition, but it didn’t dampen the spirits of the students or the Fictiv advisors. Andreev adds, “I’m proud of the huge effort the entire team brought forth and how we were able to push to the very end and not give up and go much further than we’ve ever gone.”
Olanrewaju agrees. “We had an incredible time working together with the students. It was amazing. I can’t wait to see how they do next year!”
“I’m proud of the huge effort the entire team brought forth and how we were able to push to the very end and not give up and go much further than we’ve ever gone.”
– Toshko Andreev, President, FEB
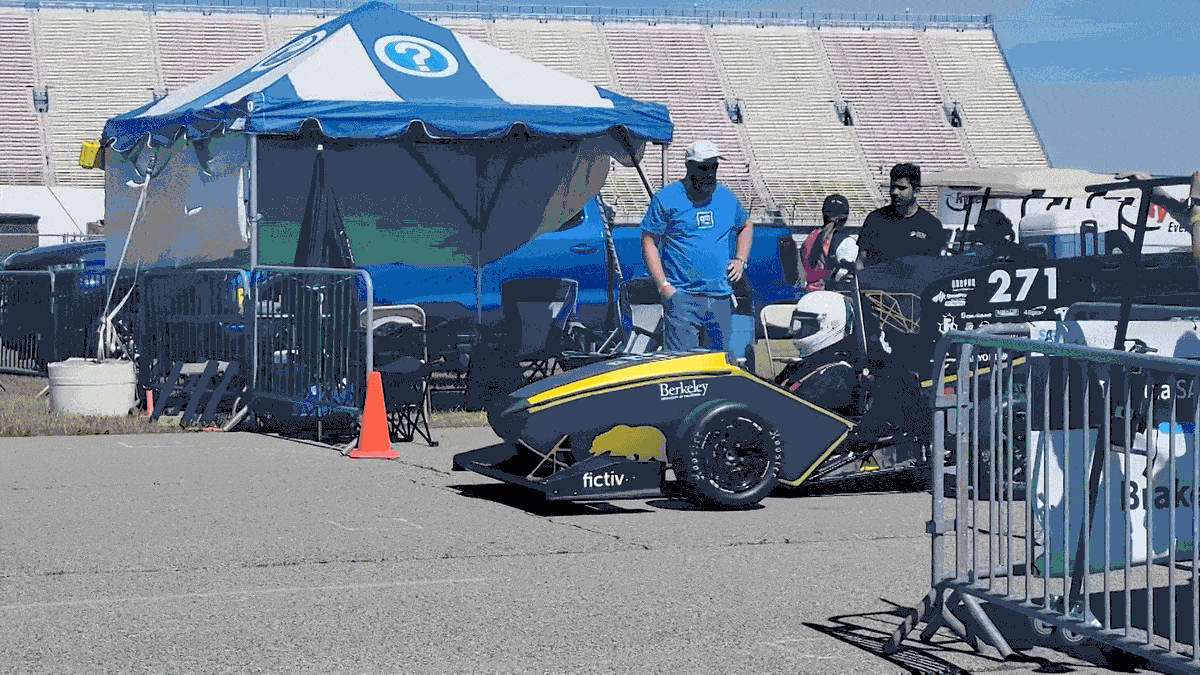
What’s Next for Formula Electric at Berkeley
What’s next for the team of young engineers? Aside from continuing participation in the Formula SAE Electric series, they’ll need sponsorship and guidance from Fictiv and other sponsors. Andreev excitedly recalled hearing a comment from one of the judges after achieving their best-ever score: “Berkeley is going to dominate next year.” His teammates matched his enthusiasm. Leafstrand goes on, “Participating in this team was so exciting. Some of the best moments of my life!”
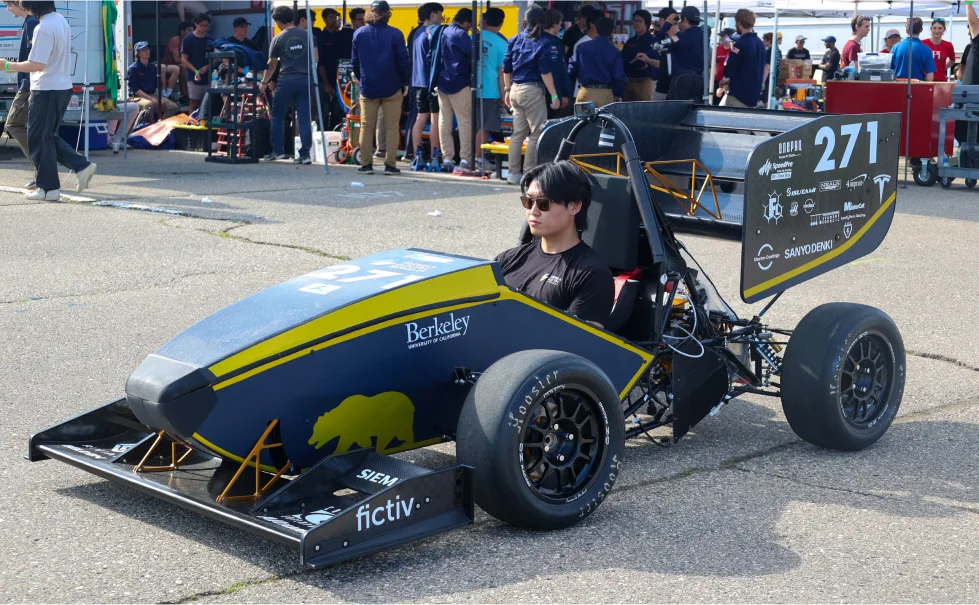
download Case Study“Participating in this team was so exciting. Some of the best moments of my life!”
– Chris Leafstrand, Chief Engineer, FEB